Common Battery Installation Issues: Insights from an Electrical Inspector
As home battery systems start to go mainstream, the focus on the safety and compliance of these systems becomes ever more critical. In this post, I will navigate the complexities of grid-connected battery system installations, uncover common challenges installers face, and underscore the pivotal role of the Australian home battery standard: AS/NZS5139:2019.
Ensuring Solar Installation Compliance
As a solar inspector, battery compliance is something I’ve only recently started to explore seriously, if I’m being honest. I’ve discovered that installers must not only possess the necessary qualifications but also undergo specialised training for each brand and product. Becoming a proficient and competent Inspector in this field requires a similar dedicated commitment; it’s a challenge!
Addressing Common Issues in Grid-Connected Battery Systems
During my relatively brief tenure inspecting grid-connected solar battery installations, I’ve encountered several recurring issues:
1. Location and Safety Zones
When installing home batteries, the placement is a critical consideration. It is important to ensure that batteries are not placed directly against or within habitable rooms unless they are installed on a surface approved for fire safety. It is also important to follow strict exclusion zone guidelines and create fireproof areas around batteries.
Materials such as terracotta, tile, brick, cement, or any substance tested to meet AS1530 standards are deemed fire-rated and suitable for battery installation surfaces. During inspections, we have encountered non-compliant installations where batteries were improperly placed under stairs, positioned too closely to windows in habitable rooms, or situated on the side of a house without maintaining the required egress distances to allow safe evacuation.
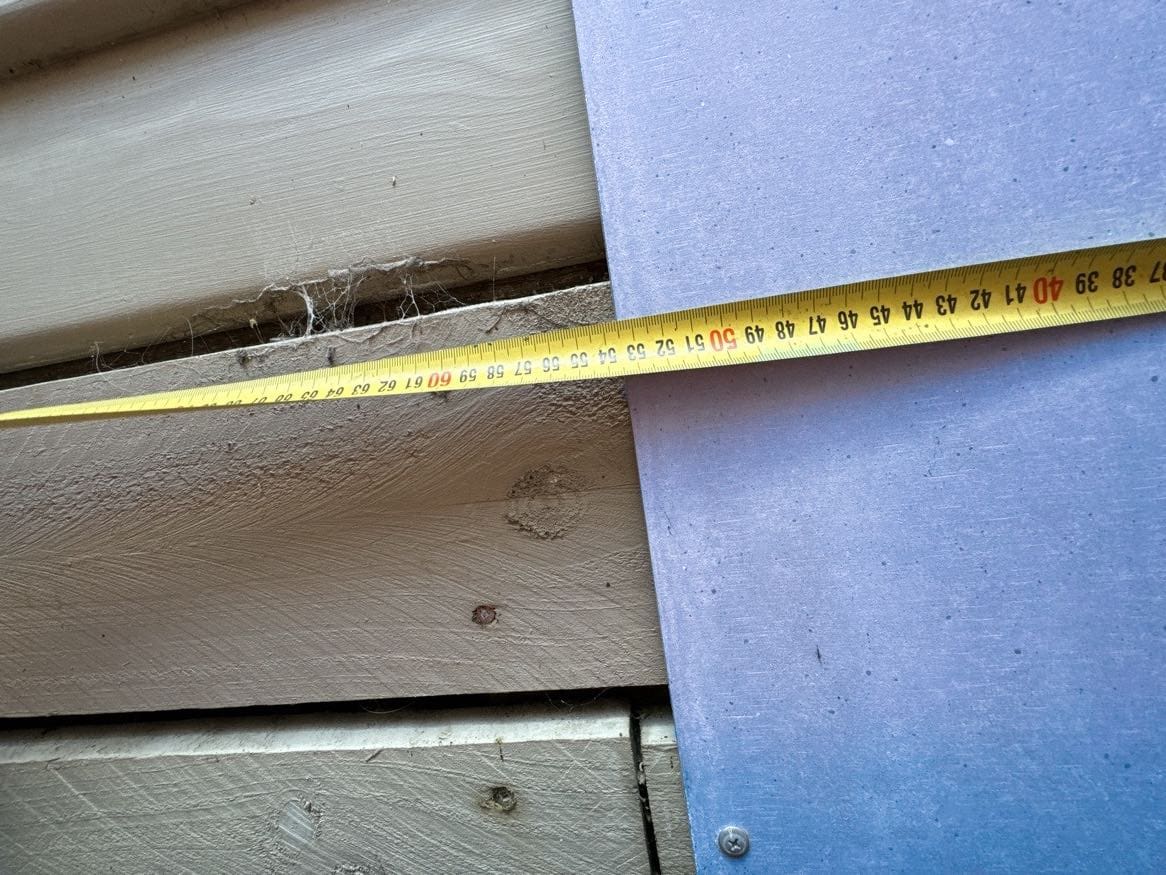
Fail: Battery located back to back with a bedroom, fire-rated material of compressed cement sheet does not extend to the minimum requirement of 600mm past the battery – exposing the non-rated material of a timber weatherboard.
2. Battery Labelling & Documentation
In the complex landscape of grid-connected battery systems, accurate labelling, signage, and documentation are crucial. Precise identification of equipment and clear instructions are not only crucial for emergency responders and maintenance personnel but are also a central focus during meticulous inspections from sticklers like me.
During inspections, we have encountered various issues, including missing toxic fumes warning labels, incomplete shutdown procedures in documentation, and oversights such as the absence of Green circular ES labels at the main switchboard or meter. Installers also get pinged when the chemistry code of the battery is either missing or inadequately displayed, and the Safety Data Sheet (SDS) isn’t in a designated position within a document holder at the main switchboard.
Labelling and documentation standards are vital for both informing emergency responders what they are dealing with and helping electricians with system maintenance and troubleshooting.
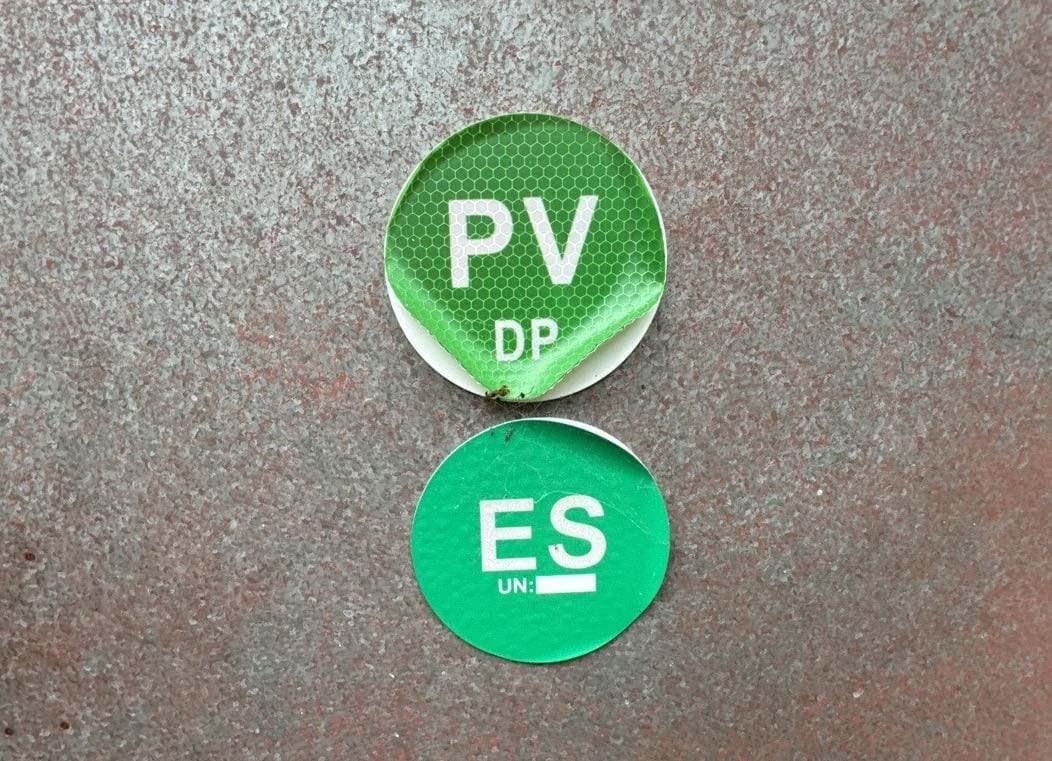
Fail: When a lithium-ion battery is installed, the number 3840 must be labelled on the ES (energy storage) label at the main switchboard/meter box
3. Overcurrent Protection Devices and Cable Sizing
Navigating cable sizing and overcurrent protection is a recurring challenge in electrical installations. Getting it wrong results in issues such as overheating, voltage drop, and compromised overall system performance. Australian Standard 5139:2019 ensures that cable sizes and overcurrent protection devices align.
Your installer must ensure that the overcurrent protection is sized at least to the battery’s capacity and then match the battery cables to the size of that overcurrent protection device.
Note to installers: While it may seem complex, rest assured that the knowledge you’ve acquired in AS/NZS3000 & 3008 is your steadfast companion. The fundamental concepts remain consistent. Additionally, remember to mechanically protect battery cables operating at voltages exceeding DVC-A with at least MD conduit.
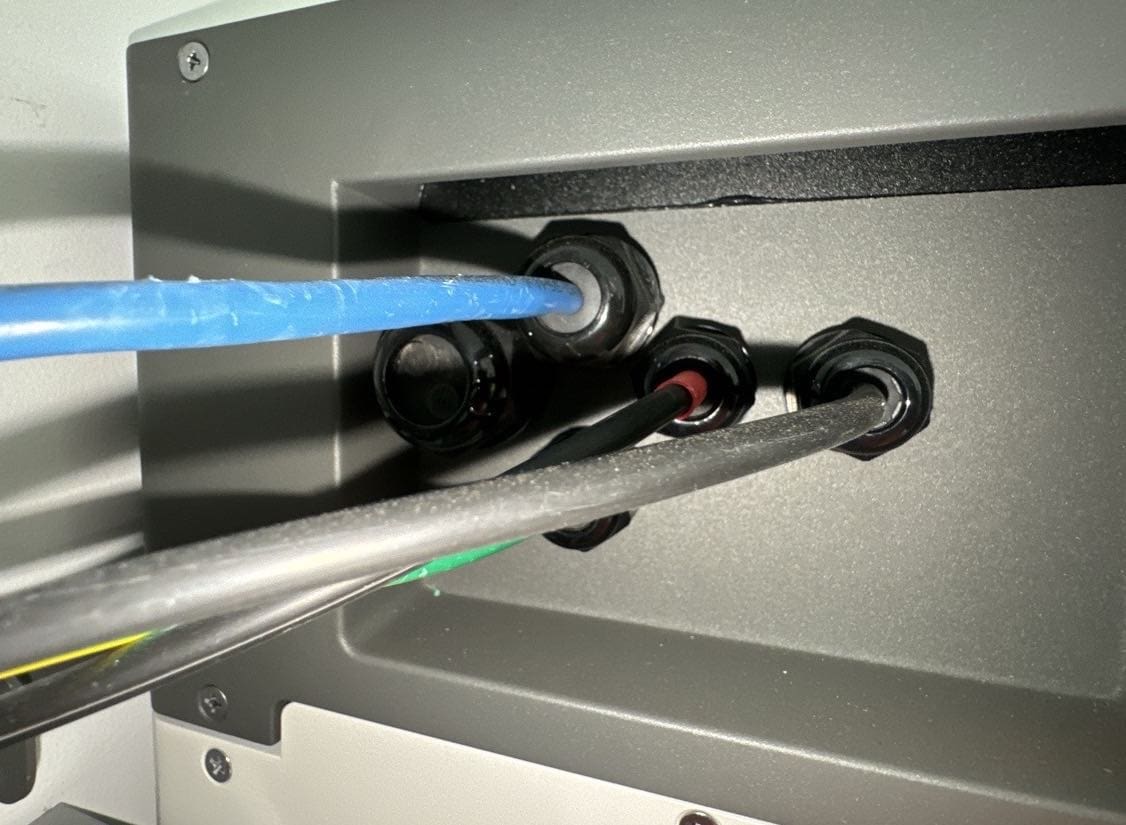
Fail: The black conductors are battery cables between a BYD battery and a Fronius inverter. The protection device protecting these cables is rated at 63 amps, which does not sufficiently protect a 10mm² cable
4. RCD Protection for Backup Circuits
Ensuring the protection of backup circuits by incorporating Residual Current Devices (RCDs) is a facet that is sometimes overlooked in the battery installation process. RCDs play a pivotal role in guarding users against electric shocks. The Standard mandates the need for such protection, placing a responsibility on inspectors to thoroughly verify its implementation during inspections.
It is essential to note that any circuits designated as backup circuits must be equipped with an RCD, regardless of their initial configuration. This requirement applies universally, irrespective of whether the circuits initially had RCD protection or not. This is a common oversight frequently missed by installers. The meticulous incorporation of RCDs into backup circuits is a non-negotiable requirement.
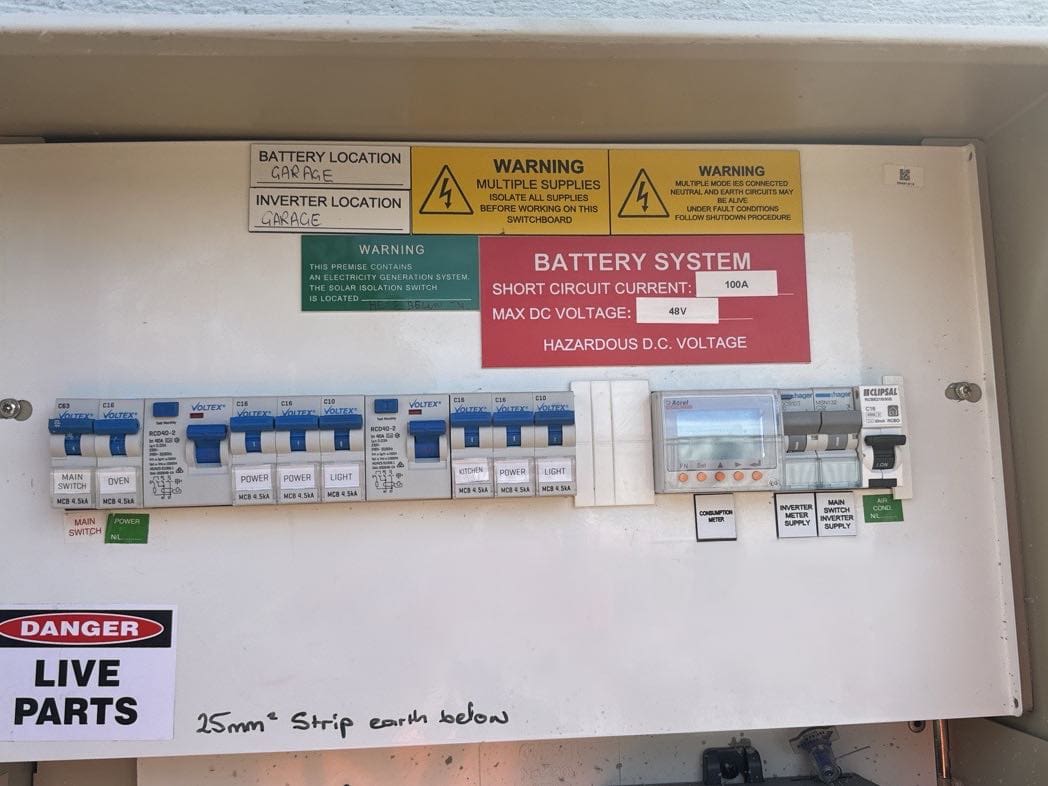
Fail: Every circuit in this switchboard is on the battery’s backup circuit. But they are not labelled as backup circuits. Also, the oven circuit does not have RCD protection
5. Mechanical Protection of Batteries
Preserving a battery’s physical integrity is paramount. Some batteries require protective bollards. The guiding principle is clear: if there exists any possibility, no matter how remote, of a battery being impacted by a vehicle, protective measures are required. Adopting a proactive approach, it is advisable to err on the side of caution.
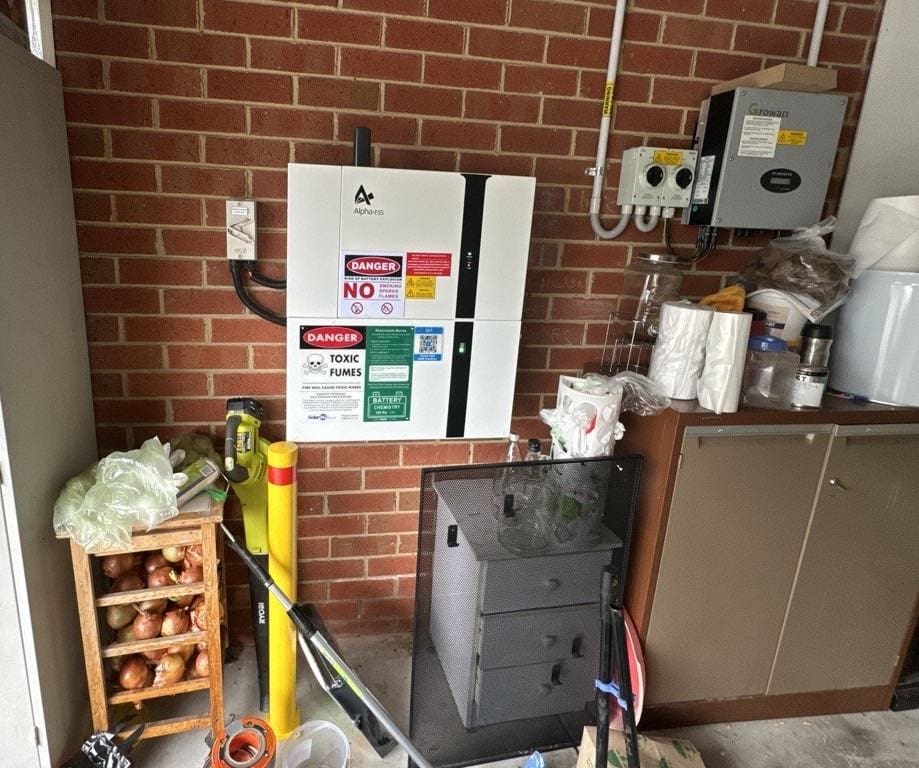
Could be improved: One bollard has been installed. A 2nd bollard would provide mechanical protection from any vehicles.
‘Section 4’ batteries leave less room for error
To avoid potential pitfalls, consider only installing a ‘Preassembled integrated Battery Energy Storage System’. In Australian Standard parlance, these are often known as ‘Section 4 batteries’ because they are dealt with in Section 4 of AS5139:2019. These systems use pre-wired batteries and battery inverters pre-assembled in their own enclosure, so the installer has less system design and installation work to do with reduced potential for errors.
This choice minimises complexity and increases the likelihood of a successful installation. However, it’s essential to receive proper training and strictly adhere to the manufacturer’s instructions. Section 5 batteries, where the batteries and battery inverter are separate, are more challenging for inexperienced installers. Section 6 batteries which comprise ‘everything else’ should generally be avoided by those lacking experience in the field.
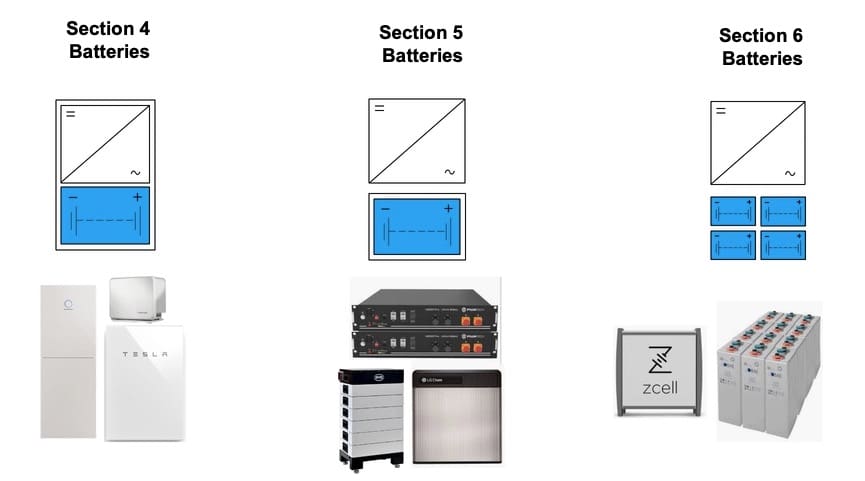
Image from CEC’s AS/NZS 5139: AN OVERVIEW
By addressing common issues related to proper location, labelling, overcurrent protection, RCD implementation, and equipment labelling, your battery installer actively contributes to a safer and more reliable industry. Through education, awareness, and adherence to established guidelines, we pave the way for a sustainable and secure battery-powered future.
Original Source: https://www.solarquotes.com.au/blog/battery-installations-insights/